From Wax to Bronze
At Denver Bronze, we take pride in bringing your unique and specific pieces to life through the fine art casting process. When you drop off your wax(es), our team of artisans will use their expertise to ensure your sculpture is cast properly.
Sometimes, this means cutting holes, known as plugs, or even cutting a piece completely in half. We know this may sound drastic, but it's necessary to make sure there's proper airflow in the shell room so that your sculpture remains hollow in bronze. It also allows us to attach the tree system, which is essential for feeding bronze directly into your sculpture. We call this process "spruing" and it involves two types of bars: feeders and vents.
Feeders attach directly to the cup, which forms a funnel for the bronze, and allow bronze to flow directly into your sculpture. Vents attach to the side of the cup or a wax bar coming off the side of the cup and help air escape as the bronze is poured. This also provides support while the sculpture is going through the shell system.
We understand that your artwork is precious to you and we treat it as such throughout the entire casting process. You can rest assured that our team is dedicated to providing the highest level of quality and care for your sculpture. We're here to help bring your creative vision to life!
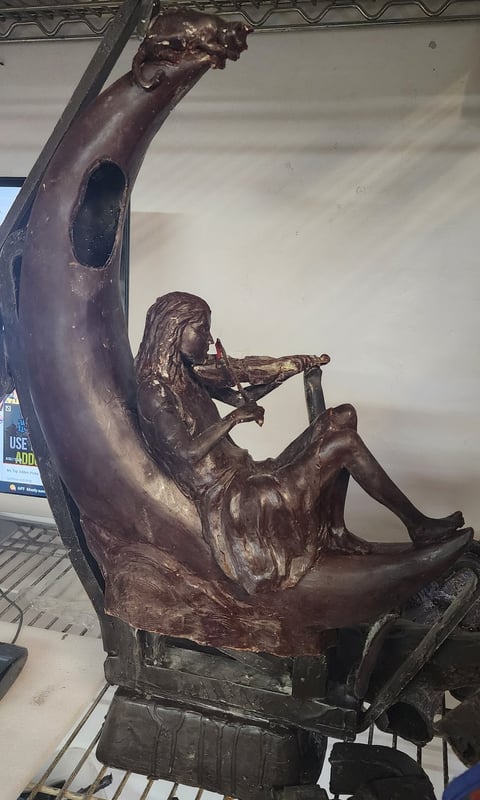
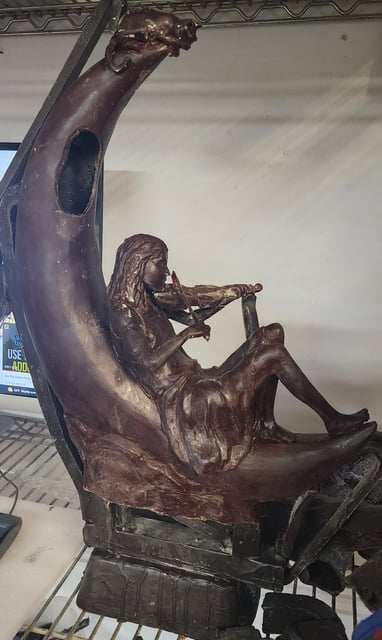
Denver Bronze's job begins when we have a wax of your sculpture.
When Denver bronze comes in:
Off to the Investment Room
To create our ceramic shells, we first apply a layer of primary binder onto the piece then coat it with sand. This process is repeated for 5-6 coats using varying grits of sand and colloidal silica to create a strong and porous surface that can withstand the casting process. Finally, we apply a coat of just colloidal silica to create a smooth finish that allows for high-quality metal parts with fine details and intricate shapes to be produced.
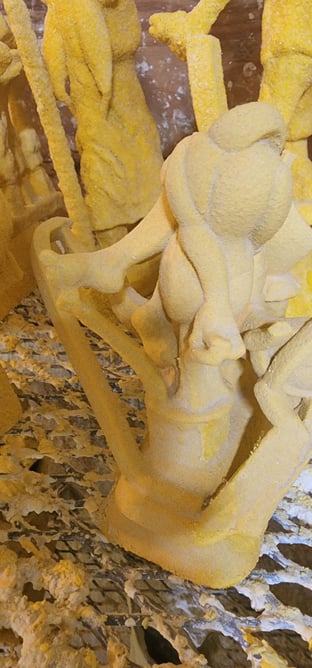
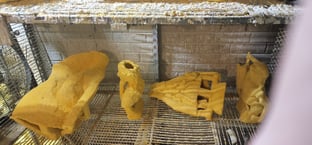
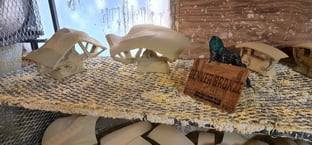
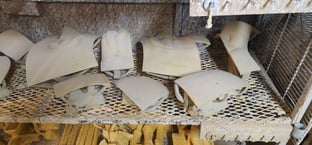
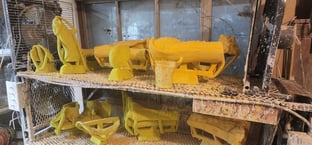
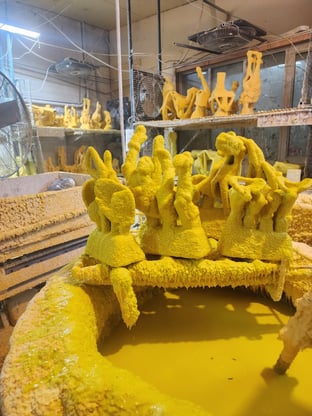
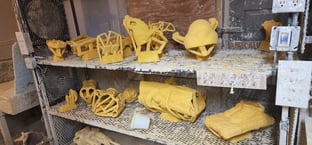
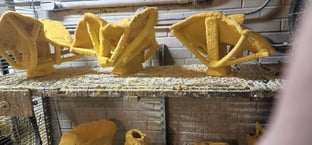
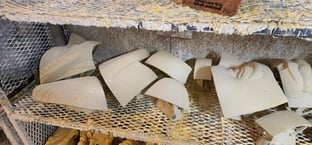
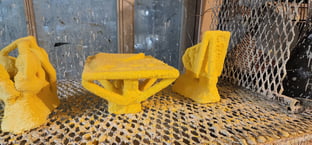
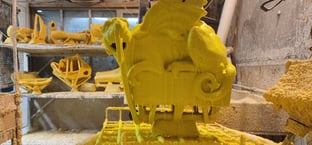
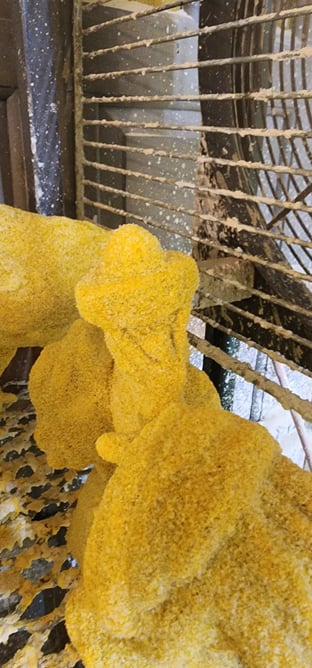
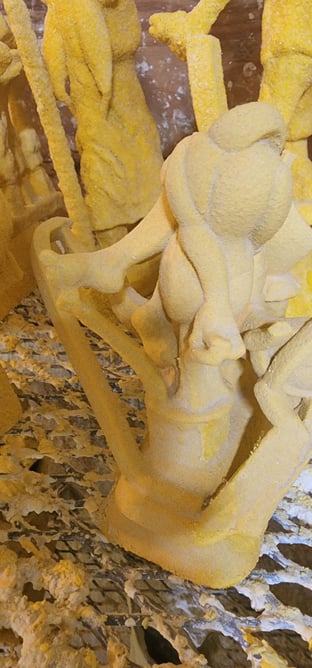
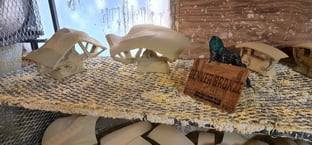
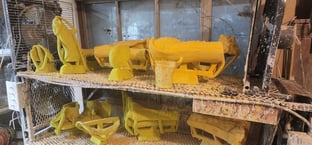
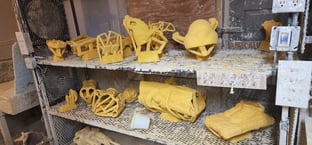
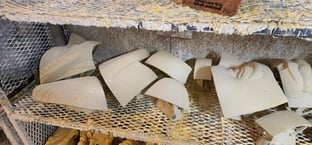
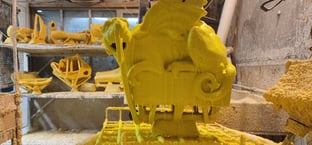
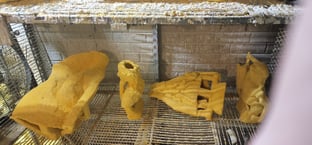
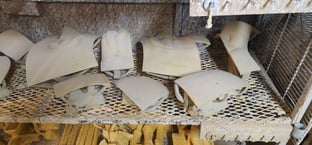
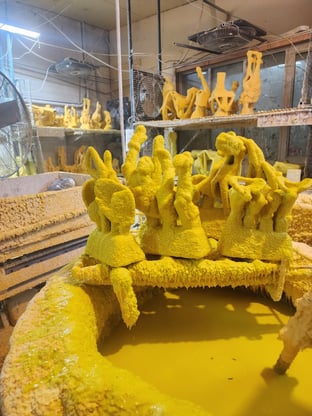
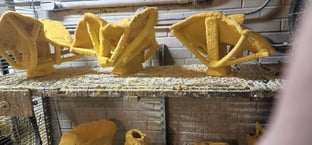
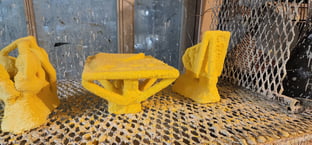
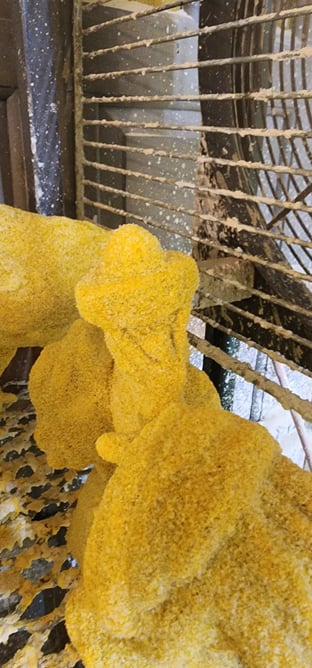
Burn Out
Now that we've finished creating the hard exterior of your sculpture, it's time to remove the wax inside. To do that, we're going to take it to a process called burnout. This involves heating the shell using 4 natural gas torches to an incredibly high temperature of 1900 degrees or more.
Once the shell is heated up, the wax inside it will melt and flow out onto a special tray made of stainless steel. This tray is designed to cool the wax quickly and direct it into metal molds where it can be collected and reused in our Foundry for future projects.

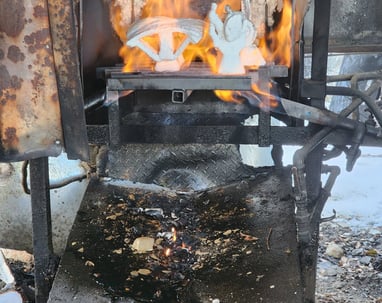
Getting ready for Bronze
After running water through the shell to check for cracks caused by the burnout process and subsiquentely fixing any cracks or issues using a high temp refractory mud it's time to head to the pre-heat. This step once again bring the shells up to 1900+ degrees, which serves two main functions. To completely dry out the shell. This step is crucial to making sure we don't create steam bombs. It also heats the shell to help the bronze flow just that much more. Once the shells are heated they are pulled red hot and placed in the sand beds and cast immediately.
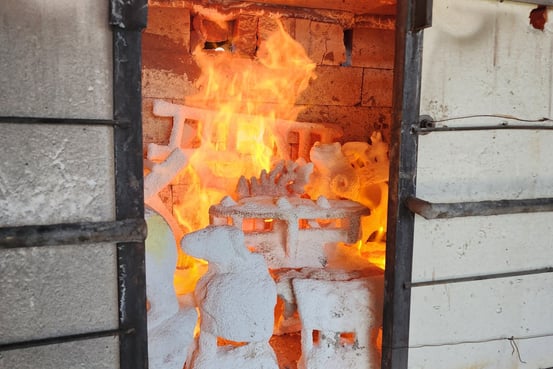
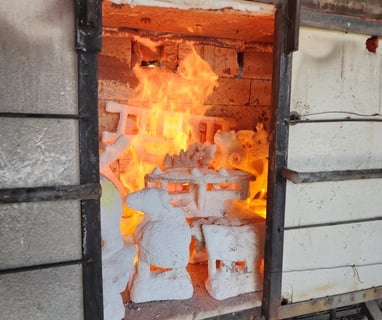
Pouring the Bronze
Here we'll take the pre-heated shells and either suspend them from forks and hang them. Or we'll place them in sand, cover the shell, and pour sand around the shell. We do this to add strength to the shell, provide an area for splashes, and should it happen, contain shell failures.
We generally use a mixture of new bronze ingots and bronze returns, which are the cups and bars from previously cast sculptures. We add borax to our bronze mixture to help clean the metal and gather impurities. The bronze is heated in our furnace using mainly using natural gas and brought to 2150 degrees.
Once cooled enough the bronzes are pulled out of the sand, quenched briefly, then the cups and bars are hammered on in an attempt to get as much shell off through vibration as possible before bringing it inside for the final steps performed by the foundry.
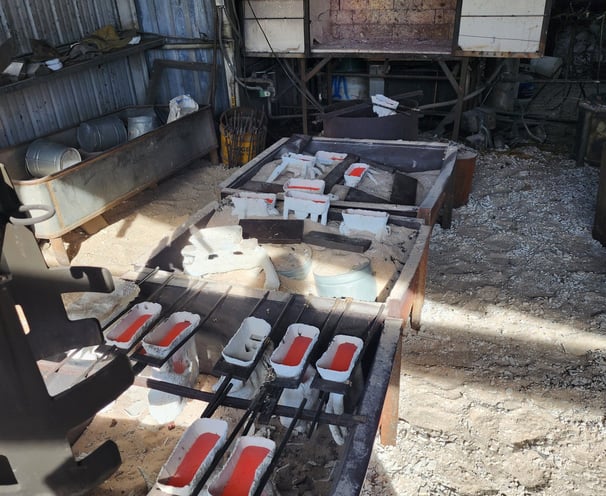
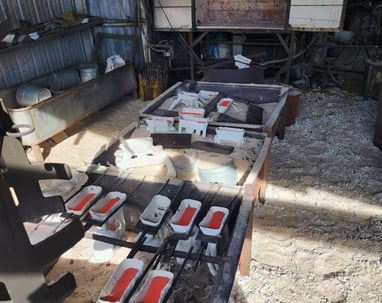
Metal Clean Up
After the bronze are cooled and roughly knocked off they are brought inside our building to the "Cut-off room". Here we'll work to remove even more excess shell using hammers and an air chisel against the cup and bars. Once we deem it clean enough, it moves over to the cut off table. Using a carbon arc rod we will remove the bars we added as close as we can safetly do so without damaging your sculpture.
The last step at Denver Bronze is to sandblast your piece. This step will remove the last remnants of the investment material and leave the bronze with an even finish.
If you need any further finishing work, there are self-employed artisans available in the building that can handle any welding, chasing or patina needs.
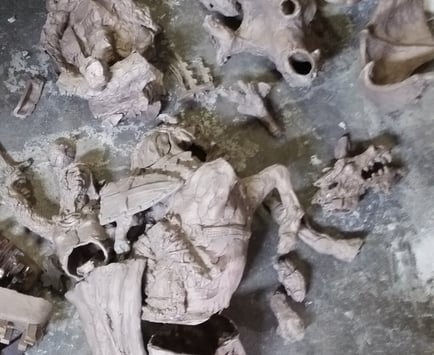
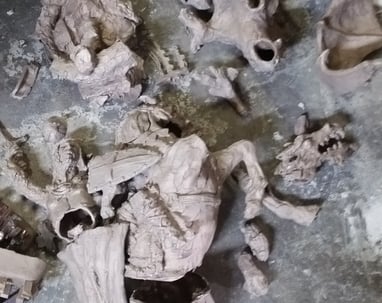